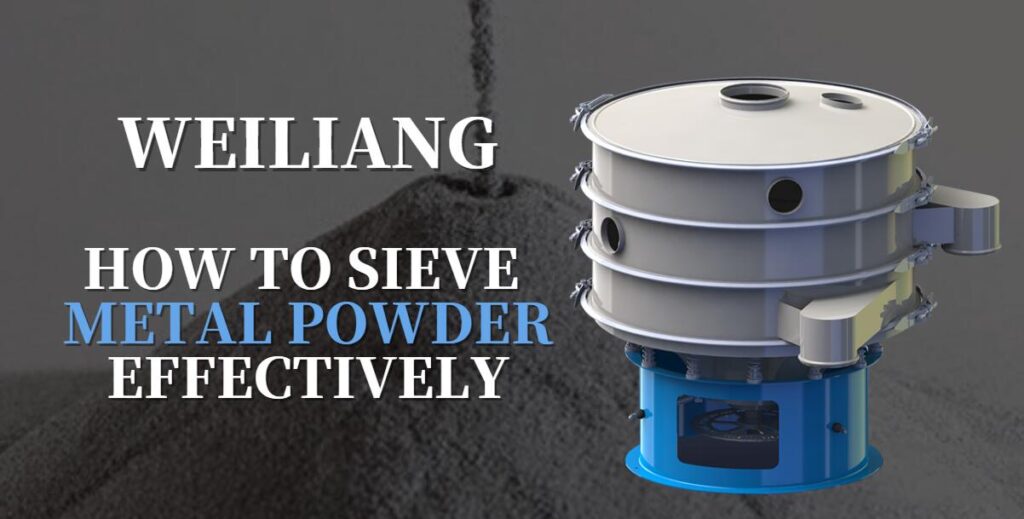
What is metal powder
Metal powder is a metal that has been broken down into a powder form. Aluminium powder, nickel powder, iron powder, and many other metals are available in powder form.
Products made from powdered metals are ones that need to be made with more precision than the traditional manufacturing processes can produce. Metal powders are used in a variety of manufacturing techniques to create metal parts. Metal powders reduce waste when compared to traditional machining and are versatile in the creation of a wide range of metal and alloy components.
Types and uses of metal powder
- Nickel powder: Used for corrosion resistance, like in the marine industry
- Tin Powder: M and SW grade tin powders are primarily used in spray-on applications for corrosion resistance.
- Aluminum powder: Fireworks, metal coatings, solar cell manufacturing in the new energy industry.
- Red and Black Cupric Oxide: Most commonly used for wood treatment and as pigments in glazes and ceramics.
- Cadmium powder: Glazed used on ceramics, transparent conductors, nickel-cadmium batteries
- Iron powder: Magnetic products, printing, brake pads, certain types of dyes and stains
- Granular Copper: Granular copper is most commonly used to make self-lubricating bearings.
- Zinc Powder: Zinc powder is incredibly versatile. It can be used to manufacture galvanized steel and to create brass. are used in the arospace industry.
- Bismuth powder: Manufacturing in batteries, welding rods, creating alloys
- Manganese Powder: Manganese powder is most often used in the steel and iron industries to create alloys for the manufacturing of tools and machinery.
Four methods to produce metal powder

1. Direct reduction is the process of combining carbon with iron oxide ore, heating the mixture, removing the sponge iron from the carbon, grinding, annealing, and regrinding the powder to make it usable for manufacturing. | 2. Gas atomization occurs when molten metal is passed through a passageway to a gas-filled chamber, where it cools. It is collected as it falls and annealed into powder. |
3. Liquid atomization is similar to gas atomization, but the metal is sprayed with high-pressure liquid, which causes the droplets to solidify faster. This makes the powder more porous, smaller, and cleaner. | 4. Centrifugal atomization happens when a metal is placed in a chamber as a rod and electrically melted at the end of the rod, resulting in melted droplets that fall into another chamber and solidify. |
Increasing demands for fine metal powder
The powder metallurgy industry has experienced massive growth in the last few years, for example the aerospace and defense industries and the additive manufacturing markets,not limited to. As a result, the market demand for finer and higher quality metal powders is also increasing.

Sieving challenges of metal powder
1. Mesh blocking
Metal powder is easy to blind the mesh and reduce the flow rate because it is particularly fine. And frequent cleaning of the screen greatly reduces the service life of the screen, causing increased downtime and loss of production.
Irregular particle shapes are also a major obstacle to metal powder sieving. They tend to wedge into the mesh aperture. In addition, due to electrostatic forces or due to the product itself, very fine powder with dust will cover the mesh and tend to agglomerate, causing blind the mesh.
2. Security issues
In addition metal powder sieving has high requirements for safety. In some explosive properties metal powder (such as aluminum powder) screening, pay particular attention to the explosion and other safety hazards.
The motor may explode in two situations. First is the surface temperature of the electric motor increase due to heating that equal the ignition temperature of the flammable matter accumulated in the factory or the industrial structure, creating an explosion. Another situation is sparks from electric motors can cause explosions within a motor’s casing that then lights the dust or liquid present in the air on fire, resulting in a bigger explosion.
3. Sealing issue
Bad sealing will cause the oxidation of metal powder, resulting in material contamination. Besides, dust leakage will create inhalation risks for the operator. In particular some toxic dusts will be harmful to their health.
How we do
1. Screen-cleaning system
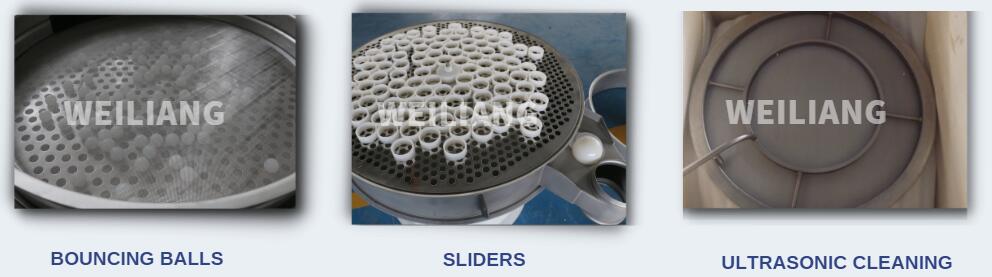
In particular, the ultrasonic system effectively prevents clogging of the mesh and promotes the passing of granules smaller than the mesh holes to improve the overall output with low amplitude and high acceleration vibration. It is designed to distribute ultrasonic vibration evenly on the resonator and screen cloth, the constant cleaning to improve screening performance.
2. Explosion-proof motor
Explosion-proof motors are designed in a specialized manner to contain any internal explosion without spreading throughout any industrial facility and creating an additional risk of fire. Weiliang usese explosion-proof motor and explosion-proof ultrasonic device to ensure safety when sieving metal powder.
3. Quality Sealing
Firstly the size of each part of the whole machine is standard with high precision. Weiliang mechanized production to improve standardization and reduce the error due to manual. Secondly, high quality gasket is used to ensure good sealing. What’s more, fully-enclosed & air-tight design is also available when air protection procedure is needed.
Our stories
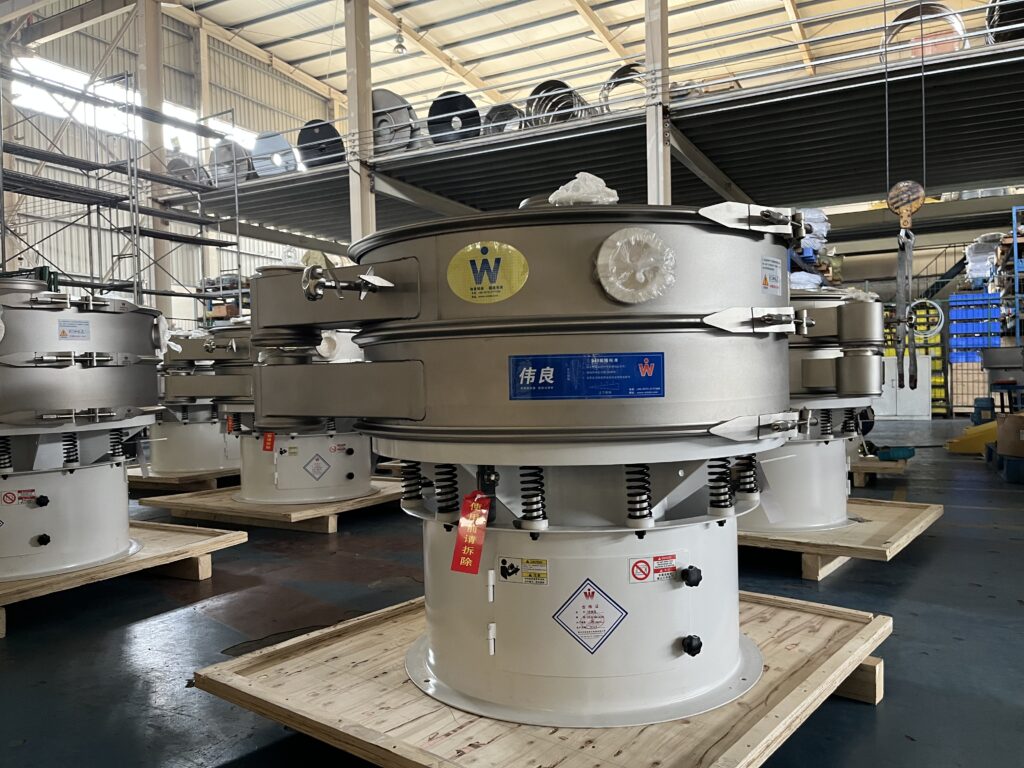
Weiliang has rich experience in metal powder sieving, materials such as aluminum powder, titanium powder, zinc powder, copper powder, iron powder, alloy powder, etc. The sieving is as fine as 20 microns. Models from S49-AC-600 to S49-AC-1500 with one or two layers.
WEILIANG will analyze each key parameter of the customer’s material based on our professional knowledge, such as particle size distribution, density, the effect of gravitational force on the product, the effect of vibrational forces, and the coefficient of friction between mesh and powder…Customize the best solution for you.
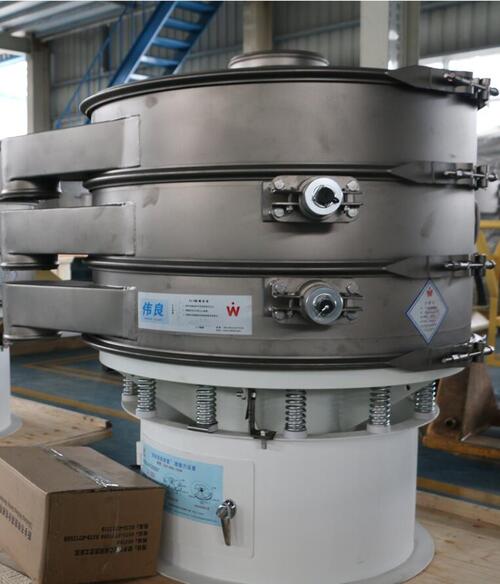
About explosion Aluminum Powder Features: explosive — explosion-proof motor & de-static device Sieving purpose: classification Sieving mesh: 160 and 200 mesh Equipment: WEILIANG S49-AC Ultrasonic vibrating screen-1 layer or 2 layers | About oxidization Titanium Powder Features: easily oxidized – good sealing Sieving purpose: classification Sieving mesh: 300 mesh Equipment: WEILIANG S49-AC Ultrasonic vibrating screen-1 layer or 2 layers |
On-site Photos
Contact us to find how our customized solutions will benefit your manufacturing process.
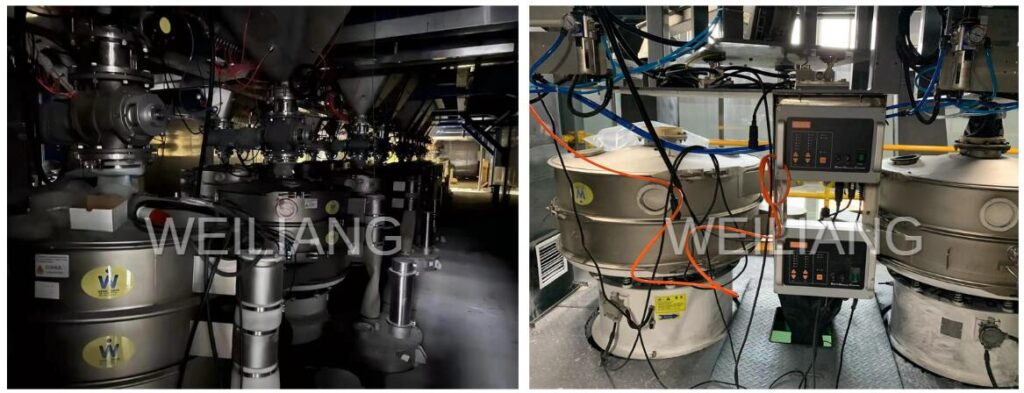
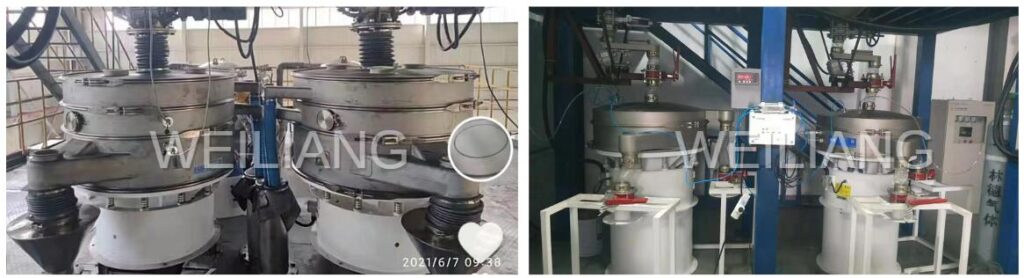
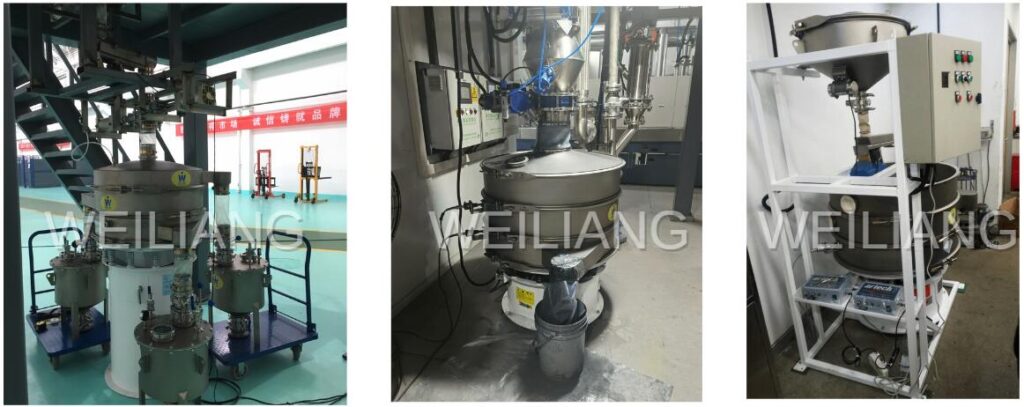