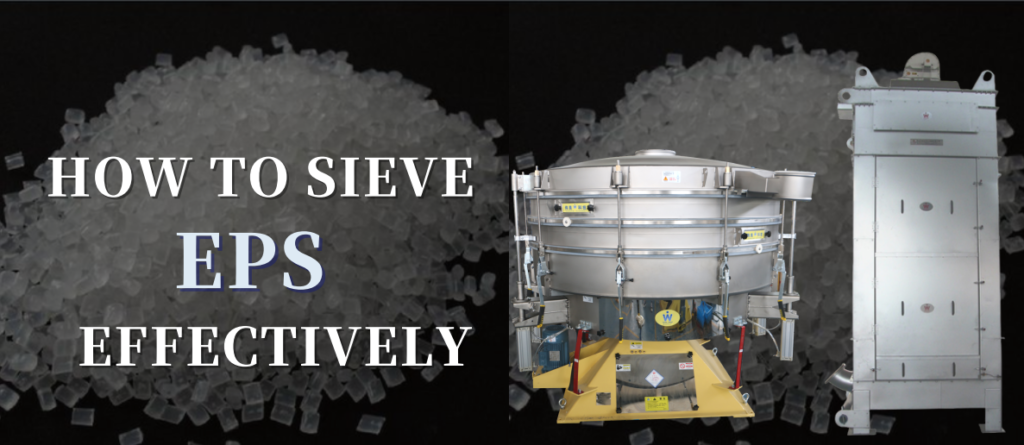
DRYING AND SCREENING EQUIPMENT IN EPS PRODUCTION LINE
WHAT IS EPS?
Expanded PolyStyrene (EPS) is a white, rigid, closed cell, lightweight thermoplastic foam material produced from solid beads of polystyrene. It produced from:
- Styrene – which forms the cellular structure
- Pentane – which is used as a blowing agent
Both styrene and pentane are hydrocarbon compounds and are obtained from petroleum and natural gas byproducts.
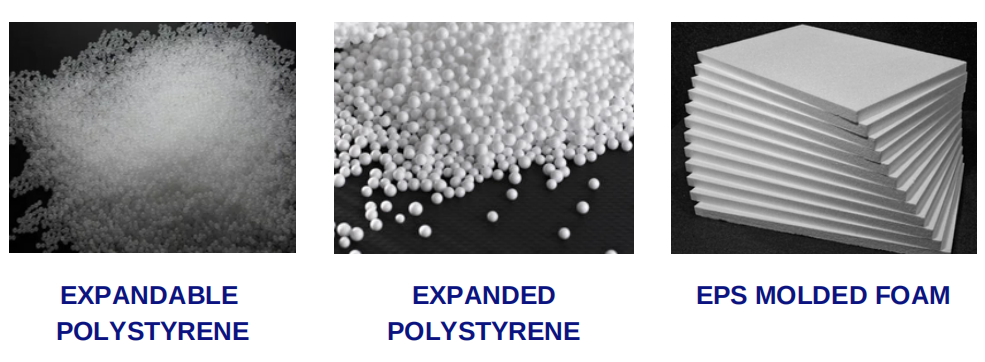
ADVANTAGE & DISADVANTAGE
Advantages of EPS • Energy efficiency and saving • Thermal resistance and insulation • Chemical inertness • Bacterial resistance • Cost-effectiveness • Sound absorption properties • Excellent impact strength & dimensional stability | Disadvantages of EPS • Poor chemical resistance to organic chemicals. • Largely Susceptible to UV radiation. • Highly Flammable. |
EPS APPLICATION
EPS is mainly used in construction and packaging.
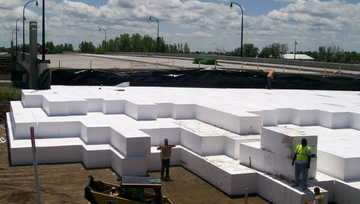
Construction and Building
Because of its insulation properties, chemical inertness, bacterial and pest resistance, EPS is widely used in the building and construction industries. Its closed-cell structure allows only a small amount of water to be absorbed. It is strong, durable and can be used as an insulated panel system for building facades, walls, roofs, and floors, as flotation material in marina and pontoon construction, and as a lightweight fill in road and railway construction.
Food Packaging
Because EPS has no nutritional value, it does not support fungal, bacterial, or other microorganism growth. As a result, it is commonly used in the packaging of foods such as seafood, fruit, and vegetables. The thermal insulating properties of EPS helps keep food fresh and prevent condensation throughout the distribution chain.
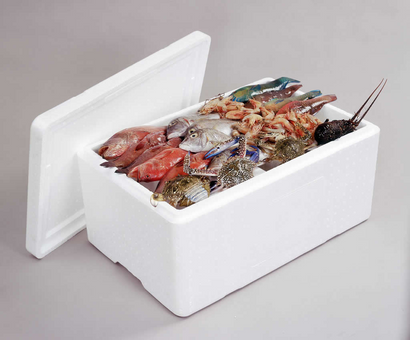

Industrial Packaging
As EPS is made of 98% air, it is one of the lightest packaging materials in existance, and therefore adds very little weight to packaging, which means transport costs and fuel emissions are kept to a minimum.
EPS packaging is often used for industrial packaging. It provides industrial products with the ideal material for complete protection and safety from risk in transport and handling thanks to its shock absorption property. This rigid lightweight foam can be molded into any shape for protecting and insulating sensitive products such as delicate medical equipment, electronic components, electrical consumer goods, toys as well as horticulture products during transport and storage.
Other Applications
- Seedling tray
- Children’s car seats
- Cycling helmets
- …
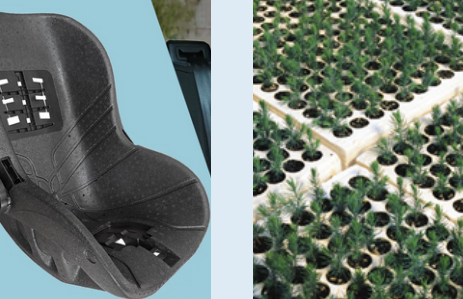
EXPANDABLE POLYSTYRENE POLYSTYRENE MANUFACTURING PROCESS
EPS generally adopts suspension polymerization. It is to disperse styrene as oil droplets under strong mechanical stirring and suspended in water with the help of suspensions, and finally polymerized into a beads under the action of initiator.

ONE-STEP METHOD OF EPS PRODUCTION
POLYMERIZATION & IMPREGNATION —- DRYING —– SIEVING —-COATING —- PACKAGING
One-step method means that styrene, initiator, dispersant, water, foaming agent and other additives are added together to the reactor for polymerization to obtain resin particles containing foaming agent. Then neutralize and wash, and then sieve after drying. Generally will be sieved into five sizes according to market requirements. Finally go to packaging.
TWO-STEP METHOD OF EPS PRODUCTION
POLYMERIZATION — DRYING — SIEVING — IMPREGNATION —DRYING —- COATING — PACKAGING
The two-step method is to polymerize styrene into a certain size of polystyrene beads, and then go to sieving. Then add water, emulsifier, foaming agent and other additives into reactor to heat for impregnation.
COMPARISON OF ONE-STEP & TWO-STEP METHODS
The difference between the two production methods is that the polymerization and impregnation take place in the same reactor in the “one-step” process, take place in different reactor in “two–step” process.
COMPARISON | ONE-STEP | TWO-STEP |
1 | Wide particle size distribution | Narrow particle size distribution |
2 | Strict process requirements and low energy consumption | Relatively low process requirements, high energy consumption |
3 | High one-time investment, high degree of automation, easy to centralize control | Relatively low one-time investment, low degree of automation, more manual operation |
4 | Short storage time due to easy volatility as foaming agent | Intermediate product PS can also be sold as final product |
EXPANDED POLYSTYRENE POLYSTYRENE MANUFACTURING PROCESS
The raw material (also known as “expandable polystyrene” or “beads”) has a round shape and resembles sugar in appearance.
The conversion process takes place in three stages.
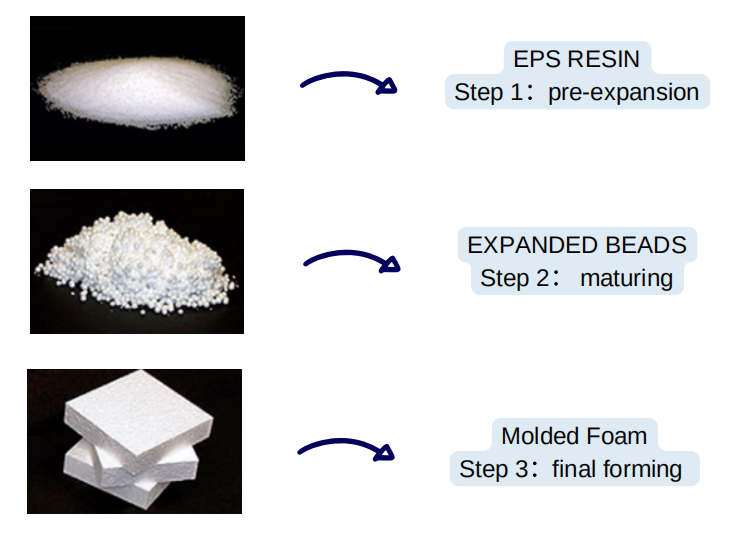
PRE-EXPANSION
The pre-foaming agent in the polystyrene beads begins to boil as the steam is heated. The beads are expanded to between 40 and 50 times their original volume, resulting in a honeycomb of closed cells.
MATURING/ CONDITIONING
After expansion the beads undergo a maturing period in order to reach an equilibrium temperature and pressure.
FINAL FORMING
The pre-expanded stabilized beads are reheated in a mould with steam. The pre-foamed beads expand further, completely fill the mould cavity and fuse together to form a shaped moulding. The beads are molded into blocks or customized products, such as panels, boards, cylinders etc. In this final form of the EPS, nearly all the volume of the EPS(~98%) is air.
WHAT WEILIANG OFFER
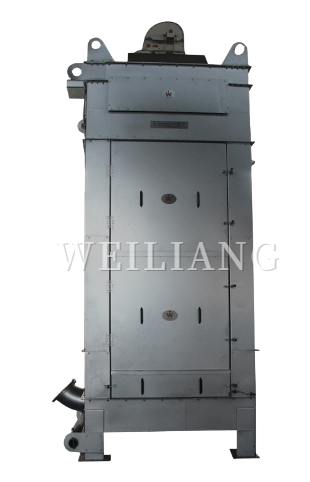
WLG EPS DRYER MACHINE
The traditional process usually uses two steps separately to achieve drying in EPS, after washing, namely centrifugal dewatering equipment and drying equipment. Weiliang, only needs one machine ( WLG EPS DRYER MACHINE ) to achieve dewatering and drying at the same time, shorten the production line.
Weiliang YBS TUMBLER SCREEN with three-dimensional adjustment system can classify EPS resin into different size with high precision and large capacity.
EPS resin is usually divided into five sizes.
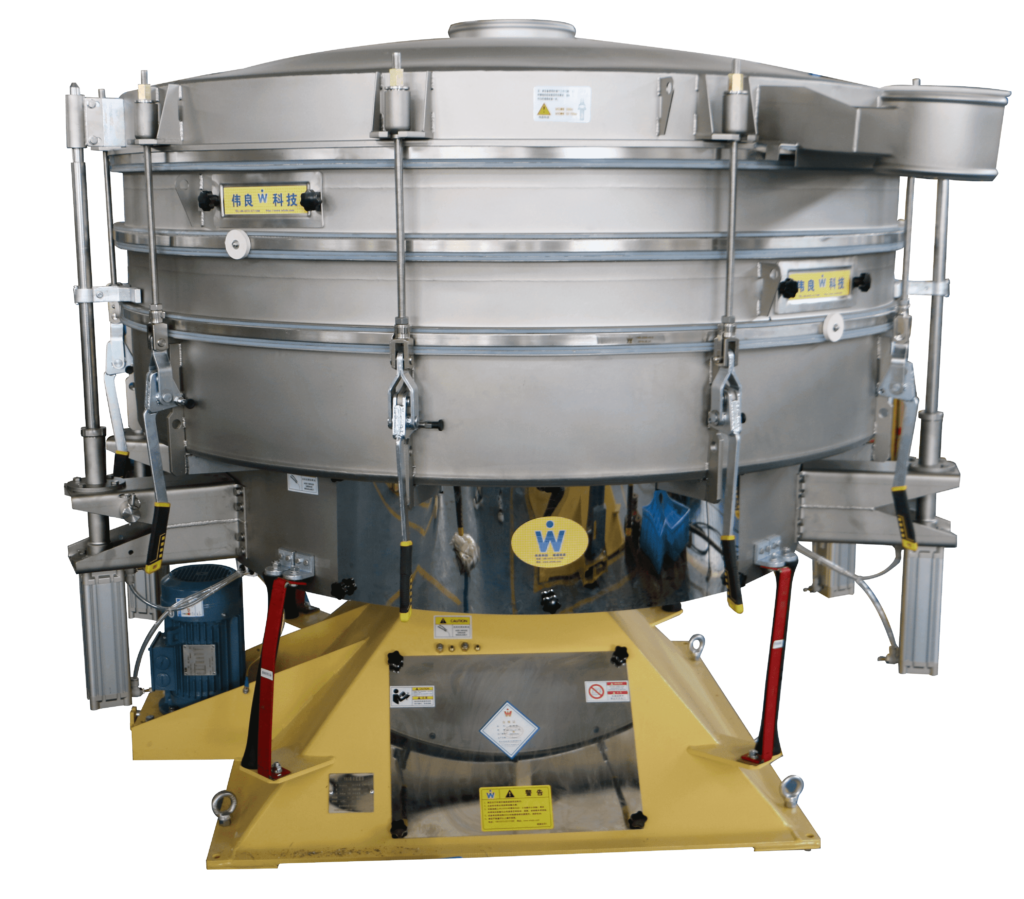
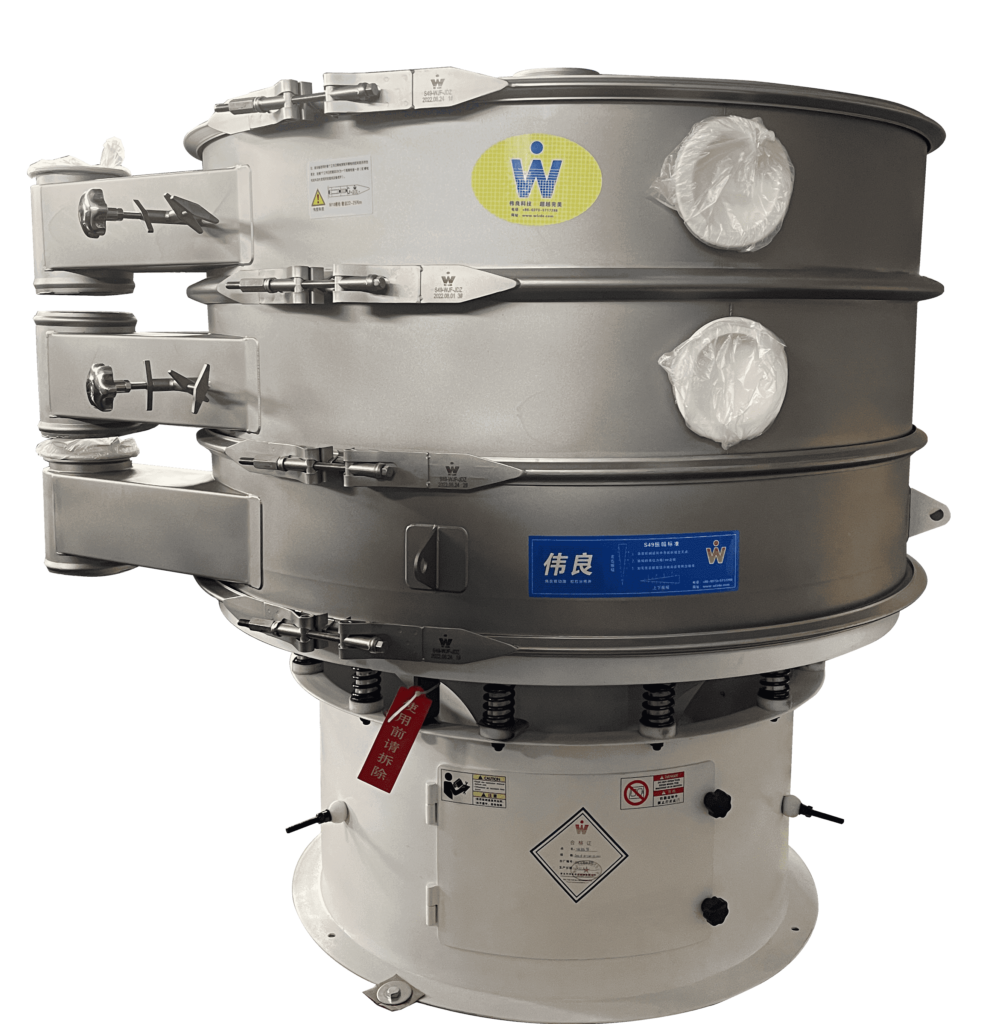
Sometimes customers will do secondary screening of oversize EPS resin (e.g. larger than 1.4 mm) coming out of the YBS tumbler screen. Weiliang S49 VIBRATING SCREEN can be set behind the YBS tumbler screen in the production line to get more size of EPS resin.
S49-AQ FLOW-THROUGH VIBRATING SCREEN
Weiliang S49-AQ FLOW-THROUGH VIBRATING SCREEN as a safety sifter to check raw materials, mainly for pre-packaging screening. Usually set before packaging for EPS inspection and impurity removal.
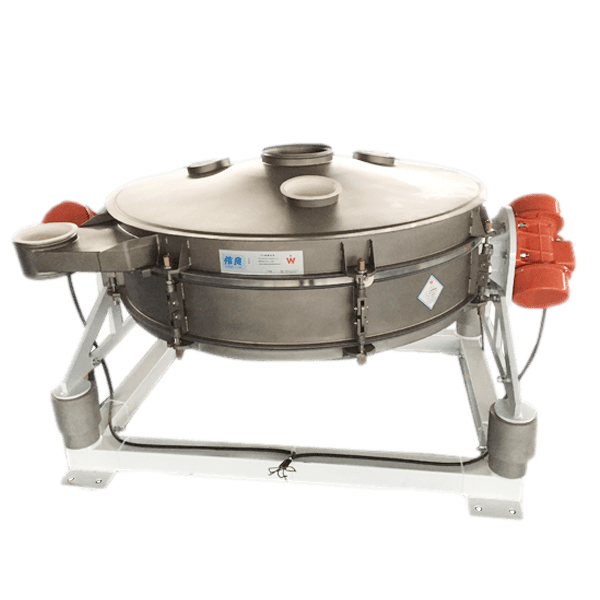
ON-SITE PHOTOS

Please feel free to contact us, let’s talk more!