
Dry mortar, refers to a granular or powdered material made by drying, screening, and physically mixing aggregates (such as quartz sand), inorganic cementitious materials (such as cement), and additives (such as polymers) in a certain proportion. It is delivered to the construction site in bags or bulk and can be used directly after adding water and mixing. It is also called dry mortar powder, dry mixed mortar, and dry mixed powder; some construction adhesives also belong to this category.
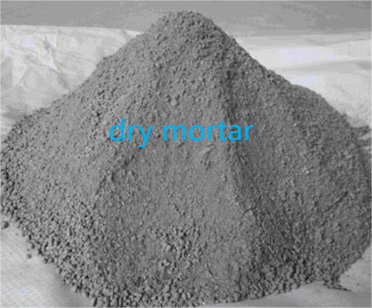
Main Components and Functions of Dry Mortar

Inorganic cementitious materials:
Generally refers to cement, such as ordinary Portland cement, which is the main cementitious component of dry-mix mortar. After adding water, a hydration reaction occurs, which gives the mortar strength and bonds the aggregates together.

Fine aggregate:
Usually sand, such as natural river sand or artificial sand. Its role is to act as a filling material, form the skeleton of the mortar, increase the volume, and reduce the shrinkage of the bonding material.
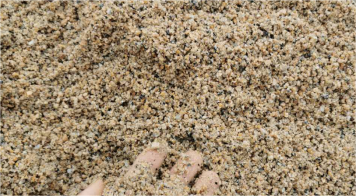
Mineral admixtures:
Common examples are fly ash and slag powder. Fly ash can improve the workability of mortar, making it easier to apply, and can also increase the later strength to a certain extent. Slag powder helps to improve the durability of mortar.

Additives:
Include cellulose ether, starch ether, etc. Cellulose ether is mainly used to improve the water retention and consistency of mortar, preventing it from losing water too quickly, which leads to poor strength development and reduced adhesion. Starch ether can enhance the anti-sagging performance of mortar, preventing it from sagging when applied on vertical surfaces.
Application of Dry Mortar
- Masonry Field
Masonry mortar is an important application of dry mortar in the construction industry. It is mainly used for masonry and various masonry constructions. It has good constructability, adhesion and water retention, ensuring the stability and durability of the masonry and meeting the requirements. Building structural strength requirements.
- Plastering field
Plastering mortar is used on the surface of buildings or building components. It is mainly used for plastering internal and external walls. It has sufficient waterproof performance and good constructability. It can reduce the number of plastering layers, improve construction efficiency, ensure construction quality, and make the plaster surface smooth and even. , has good crack resistance and impermeability properties.
- Tile adhesive field
Tile adhesive is a special dry mortar product for ceramic tile installation. It is mainly used for bonding ceramic tiles, polished tiles, granite and other natural stones. Ceramic tile adhesive has advanced construction technology, good anti-sag performance and high bonding strength, which can significantly improve construction quality and efficiency. At the same time, it can save material usage, achieve thin-layer bonding, and reduce project costs.
- Insulation Field
Thermal insulation mortar is an application of dry mortar in the field of thermal insulation. It is mainly composed of polystyrene particles, cellulose, rubber powder, fiber and other additives and has thermal insulation properties. Insulation mortar can be used by just adding water and is easy to construct; it has high bonding strength, is not easy to hollow or fall off, has stable physical and mechanical properties, low shrinkage, and is not easy to crack or crack; it can be constructed on wet surfaces, has fast drying speed and a short construction period.
- Floor Field
Floor mortar is a special product of dry mortar used in floor construction. It is mainly used for leveling and laying floors. It has the characteristics of high compressive strength, low shrinkage and good adhesion. The floor mortar can be pumped after mixing with water and is easy to use; it can be quickly constructed over a large area, saving labor costs; it can automatically level the surface to make the construction surface smooth and smooth, reducing the load on the building; it has the characteristics of rapid solidification, which can shorten the construction period.
- Other areas
In addition to the above fields, dry mortar can also be used for grouting, interface treatment, decoration, etc. Grout is used to fill the joints between ceramic tiles or natural stones; interface mortar is used to firmly bond the base material and surface material; decorative mortar and powder coating can be used for architectural decoration.
Generally speaking, dry mortar has broad application prospects in the construction industry. With the development of the construction industry and the continuous improvement of construction quality, efficiency, environmental protection and other requirements, dry mortar will be more widely used and promoted.

Industry Analysis of Dry Mortar
According to the latest research by QYResearch, the global dry mortar market achieved sales revenue of 195 billion yuan in 2022, and is expected to reach 240 million yuan by 2029, with a compound annual growth rate (CAGR) of 3.02% from 2023 to 2029. The top three companies in the global market are Sika, Saint-Gobain Weber, and Henkel.

(Source: Third-party data, news reports, interviews with industry experts, and research compiled by QYResearch, 2023)
In 2022, China’s dry mortar market revenue is about RMB 42.867 billion, and is expected to reach RMB 56.687 billion by 2029. We expect the compound annual growth rate (CAGR) of China’s dry mortar revenue to be 4.11% from 2023 to 2029.
At present, dry mortar is mainly divided into facing type, bonding type and other types, among which bonding type is the main type and future trend. In 2022, the global bonding dry mortar market size will be 17.545 billion yuan, accounting for about 40.93% of the Chinese market.
The implementation of China’s building energy-saving goals ensures a strong demand for mortar. With the improvement of people’s living standards, the requirements for building quality are getting higher and higher. The use of dry mortar can greatly improve the quality of the project. The dry mortar production line equipment has greatly solved the problems of large wall masonry, poor wall flatness, and large amount of plastering in my country. In short, the development prospects of dry mortar in the construction industry are very promising.

Current Trends in Dry Mortar Industry
Market demand continues to grow
- Driven by the development of the construction industry: With the continuous advancement of various construction projects such as urban infrastructure construction, real estate projects, and industrial buildings in China, the demand for dry-mix mortar has also continued to increase. Whether it is a new construction project or the renovation and maintenance of existing buildings, a large amount of dry-mix mortar is required. For example, in urban rail transit, large commercial complexes, etc., the use of dry-mix mortar is very large.
- The rise of prefabricated buildings: The rapid development of prefabricated buildings in recent years has created a huge demand for supporting dry-mix mortars for component connection, sealing, filling, etc., which has brought new market opportunities to the dry-mix mortar industry. Compared with traditional buildings, prefabricated buildings have higher requirements for the quality and performance of dry-mix mortars, which has promoted the technological upgrading of the industry.
Increase in product variety
- Functional diversification: In order to meet the needs of different building components and construction processes, the product types of dry mortar are becoming more refined and diversified. In addition to the common masonry and plastering mortar, there are also special mortars such as waterproof mortar, thermal insulation mortar, self-leveling mortar, and repair mortar to solve specific construction problems and improve building quality and performance.
- Favor green and environmentally friendly products: As environmental protection policies become more and more stringent and people’s environmental awareness becomes stronger, green and environmentally friendly dry-mix mortar has become a development focus. For example, dry-mix mortar produced using industrial waste slag, tailings, etc. as raw materials can reduce costs, reduce environmental pollution, and meet the goals of sustainable development.
Accelerate technological innovation
- Production technology improvement: Dry mortar manufacturers are increasing their investment in production technology research and development to improve efficiency and product quality. For example, the use of advanced automated production equipment and control systems can accurately control and intelligently manage the production process, reducing errors caused by manual operations. In addition, optimizing the production process can improve raw material utilization and reduce production costs.
- Formula research upgrade: Scientific research institutions and enterprises continue to strengthen the research on dry mortar formulas, and continuously improve product performance by adding new additives and improving bonding materials. For example, they develop products with higher bonding strength, better crack resistance and stronger water resistance to meet the construction industry’s demand for high-quality mortar.
Industry concentration gradually increases
- More mergers and acquisitions: As market competition intensifies, small companies with weaker technical strength face survival pressure, while large companies expand their market share through mergers and acquisitions, strategic cooperation, etc., and the industry concentration continues to increase. Large companies have advantages in capital, technology, and brand, and can better respond to market changes and provide customers with better products and services.
- Accelerate the construction of industrial parks: Various places have established dry mortar industrial parks to encourage enterprises to gather. Enterprises in the parks can share infrastructure, technology research and development, logistics and other resources, reduce operating costs and enhance competitiveness. In addition, the construction of industrial parks is conducive to strengthening industry management, regulating market order and promoting the healthy development of the industry.
Intelligent application expansion
- Smart production: Integrate technologies such as the Internet of Things, big data, and artificial intelligence into the dry mortar production process to achieve remote monitoring, fault warning, and intelligent maintenance of production equipment, and improve equipment operation stability and reliability. Real-time data collection and analysis optimizes production processes and plans, and improves production efficiency and product quality.
- Smart construction: During the construction process, the use of smart equipment and tools can achieve precision and automation of dry mortar. For example, using smart spraying equipment for mortar spraying can not only improve construction efficiency, but also ensure the uniformity and stability of construction quality.
Accelerate international development
- Exports increased: With the continuous improvement of the technical level and quality level of China’s dry mortar products, the international competitiveness has been continuously enhanced, and the export volume has gradually increased. Some companies have actively expanded overseas markets, and their products have been exported to Southeast Asia, Africa, the Middle East and other regions to participate in international market competition.
- International cooperation continues to strengthen: Domestic enterprises are increasingly cooperating with internationally renowned enterprises, introducing foreign advanced technology, management experience and capital to enhance the overall strength of enterprises. At the same time, domestic enterprises actively participate in the formulation of international standards to enhance the influence of China’s dry mortar industry on the international stage.

Production Process of Dry Mortar
The production process of dry mortar can be divided into three stages:
- Raw material pre-processing: This stage involves crushing, drying and screening raw materials such as sand. Proper pre-processing ensures that the raw materials meet the required specifications for quality and consistency.
- Weighing, proportioning and mixing of various raw materials: In this stage, different raw materials are accurately weighed and proportioned according to the specific recipe. They are then mixed thoroughly to ensure a uniform mix, which is crucial for the performance of the final product.
- Intermediate storage, packaging and distribution: After mixing, the product is temporarily stored and then packaged. The packaging process ensures that the dry mortar is protected from moisture and contamination. Finally, the packaged product is transported to various distribution points for delivery to the construction site.
This systematic approach to production helps maintain the quality and reliability of dry-mix mortars that meet the needs of the construction industry.
In the production process of dry mortar, the most critical link is the uniformity of sand processing and mixing, especially the screening and drying of sand. Among them, the biggest difficulty in the screening link is how to achieve reasonable gradation of sand particle size while improving efficiency, which puts high demands on production equipment. In response to this problem, we have specially designed a dry mortar screening equipment, which is our Weiliang gyratory screen.
Importance of Dry Mortar Screening
- Ensure reasonable particle size distribution:
Aggregates (e.g. sand) in dry mortar with large differences in particle size will seriously affect the workability of the mortar. Screening can separate the aggregates into different particle sizes and then mix them in specific proportions to achieve the best particle size distribution. - Remove impurities and oversized particles:
During the mining or transportation process, the raw materials of dry-mix mortar may be mixed with impurities such as soil and stones. Screening can effectively remove these impurities. For example, soil impurities in sand and gravel will affect the bonding properties of the mortar and reduce the bonding strength between the mortar and the substrate or masonry materials. In addition, oversized particles that have not been screened may cause pipe blockage during mechanized construction (dry-mix mortar is transported through pipes), affecting the flatness of the mortar surface and causing unevenness during plastering or ground leveling. - Ensure stable and uniform product quality:
Dry mortar is mixed in a certain proportion, and screening is an important step to ensure its quality stability. Different batches of raw materials have differences in properties such as particle size. Screening helps to standardize these materials and ensure that each batch of dry mortar has similar physical properties, such as density and fluidity. In construction projects with strict quality control, the use of screened dry mortar can ensure the consistency of quality in applications such as wall masonry and wall plastering, and avoid problems such as wall cracking and plaster layer shedding due to fluctuations in mortar quality. - Enhance the effectiveness of additives:
Dry-mix mortars often contain additives such as cellulose ethers and starch ethers to improve their properties. When the particle size of screened dry-mix mortar is uniform, these additives can be more effectively dispersed throughout the mortar. For example, cellulose ethers can evenly coat the surface of mortar particles, maximizing their water retention and thickening effects. Without screening, uneven particle size may cause additives to concentrate around certain particles, preventing them from working evenly throughout the mortar system, which can adversely affect the overall performance of the mortar.
In summary, screening is an important process in dry mortar production that ensures optimal particle grading, removes impurities, maintains consistent product quality, and improves the effectiveness of additives, all of which contribute to the overall performance and reliability of the final product.

Screening Case of Dry Mortar
In the production process of dry mortar, screening is a key link to ensure product quality and performance. The following is a specific screening case, showing how to improve the production efficiency and quality of dry mortar through effective screening technology.
Background
When a building materials company was producing dry mortar, it found that the workability and bonding properties of its products were unstable, which led to wall cracks and plaster layer shedding during construction. After analysis, it was found that the problem was mainly caused by the uneven sand particle size and the presence of impurities in the raw materials.
Screening Solutions
1) Device selection:
- The company decided to introduce the Weiliang square swing screen, a screening device specially designed for dry mortar. The device can efficiently separate sand into different particle size grades and remove impurities.
2) Screening process:
- Raw material pre-treatment: Before screening, the sand is crushed and dried to ensure that its moisture content and particle size are suitable for screening.
- Screening operation: Use the Weiliang gyratory sifter for screening, set the appropriate screen aperture to separate sand of different particle sizes. During the screening process, the swinging motion of the equipment makes the sand evenly distributed on the screen, ensuring efficient grading effect.
- Impurity Removal: During the screening process, impurities such as soil and stones are effectively removed to ensure the purity of the sand.
3) Results Analysis:
- Improved particle size uniformity: After screening, the particle size distribution of the sand is more reasonable and the particle grading reaches the optimal state.
- Product quality improvement: The workability and bonding properties of dry-mix mortar produced using screened sand are significantly improved, and the construction quality is guaranteed.
- Reduce construction problems: Due to the removal of impurities and oversized particles, pipe blockage during construction is greatly reduced, and the surface smoothness of plastering and floor leveling is also improved.

In conclusion
By introducing efficient screening equipment and optimizing the screening process, the building materials company successfully solved the quality problems in the production of dry mortar. Screening not only improves the quality of raw materials, but also ensures the stability and reliability of the final product, providing strong support for the company’s market competitiveness. This case demonstrates the importance and practical application effect of screening in the production of dry mortar.
Contact us for more details!