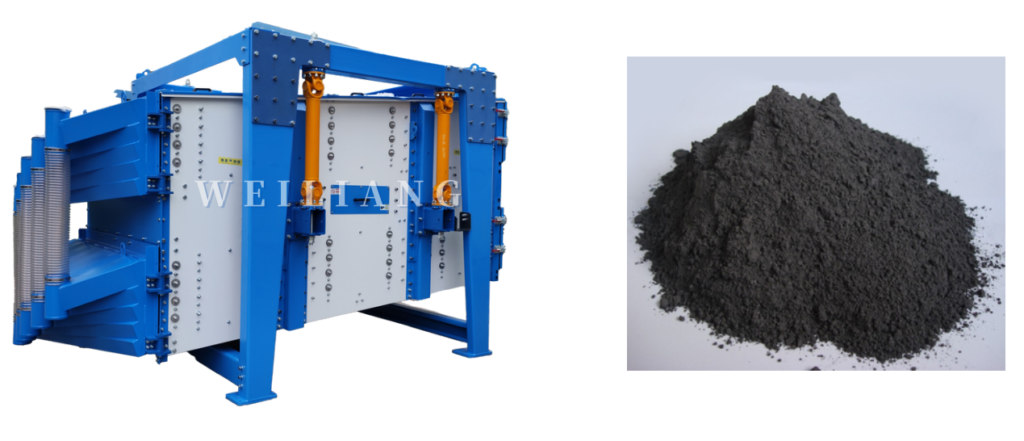
WHAT IS SILICON
Silicon is a non-metallic element of the carbon family having atomic number 14 and is represented by the atomic symbol Si. It is a tetravalent metalloid and semiconductor that has a bluish-grey color and is hard, brittle, and lustrous. Silicon is the second most abundant element on earth after oxygen and makes up around 27.7% of the crust. It rarely occurs as a monomer in nature, but as a complex silicate or silica, which widely found in rocks, gravels and dust.
USES OF SILICON
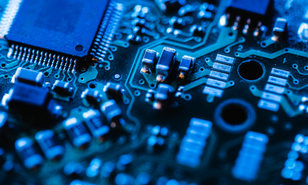
1. Electronics
High-purity silicon is created by thermally decomposing the ultra-pure trichlorosilane. After this, silicon is recrystallized, which is utilized to make many different kinds of electronics, including integrated circuits, transistors, printed circuit boards, and semiconductors.
2. Solar panels
Due to silicon wafers’ semiconducting characteristics and their abundance, they are typically used in the production of solar cells
and solar panels.
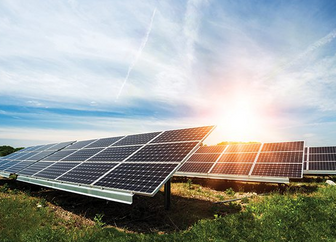
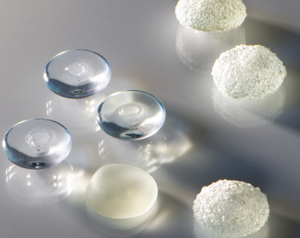
3. Silicone
Silicone oil is typically used as a lubricant added to create cosmetics, hair conditioners, and shampoos. Silicone can also be used to create rubber for waterproof sealants in washrooms and windows, pipes and roofs. Silicone is used to make the casings for
electrical appliances because it is a strong insulator. In the medical industry, silicone is used in certain implants, catheters, contact lenses, and bandages.
4. Construction Industry
Sand and clay are the compounds of silicon that are majorly used at construction sites. Silica also forms the major constituent of Portland cement along with calcium. It is used in making
building mortar as well as stucco.
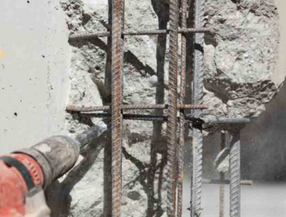
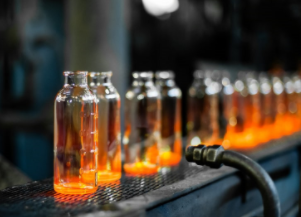
5.Ceramics
Silica is used as a constituent element of several varieties of ceramics. Porcelain’s main component is a silicate mineral called kaolinite. Traditional soda-lime glass, which is used for containers and window panes, also contains silicon compounds. A variety of glass fibers with a silica basis make up optical fibers.
Additionally, glass wool, used for thermal insulation, fiberglass, used to provide structural support, is also silica-based compounds.
HOW SILICON IS PRODUCED
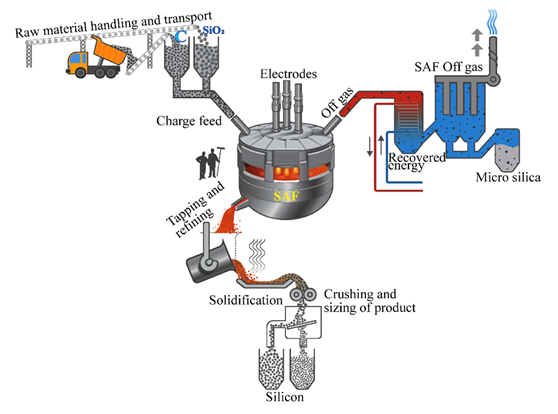
Image reference Schei et al. 1998 (A. Schei, J. K. Tuset, and H. Tveit. Production of high silicon alloys. Tapir Trondheim, Norway, 1998.)
REDUCTION PROCESS—- COOLING/CRUSHING—– PACKAGING
Silicon is commercially prepared by reduction of silicon dioxide with carbon in a submerged arc furnace (SAF); a schematic drawing illustrating the process. The illustration shows the furnace surrounded by raw material – and power supply system, off-gas removal – and heat recovery equipment, tapping, casting and crushing.
The fundamental procedure involves heating silica and coke to high temperatures in a submerged electric arc furnace. High temperatures are required to produce a reaction where the oxygen is removed, leaving behind silicon. It’s called a reduction process. Liquid silicon is tapped from the bottom of the furnace. After tapping, the liquid silicon is refined by slag treatment or gas purging. Then the liquid silicon is poured into suitable molds, allowed to cool down and then crushed to the desired particle sizes.
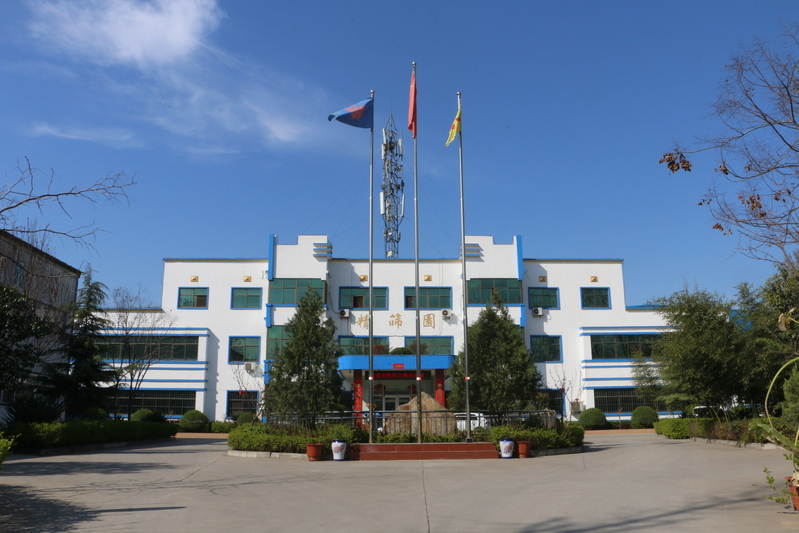
SILICON POWDER
Metallurgical silicon is typically produced in a size of 0-100 mm, but for most applications further size reduction is required. The optimum particle size depends strongly on the final application.
Silicon powder is produced by crushing, milling and classifying silicon material to obtain the required particle size.
Silicon powder, also referred to as micronized silicon, has a wide range of uses.
Main applications for silicon powder include the following:
- Semiconductors
- Refractory Materials
- Adhesives & Coatings
- Silicone Rubbers, Oils, and Resins
- Lubricants
In addition to the many uses already mentioned, silicon powder can also be utilized to make medications, food, and beverages, as well as in biomedical applications. The purity and grain particle size of the silicon powder will determine the kind that is added to other base metals and applications.
Weiliang not only provides screening equipment for classifying silicon powder into different sizes, but also provides services for the whole industrial chain of industrial silicon.
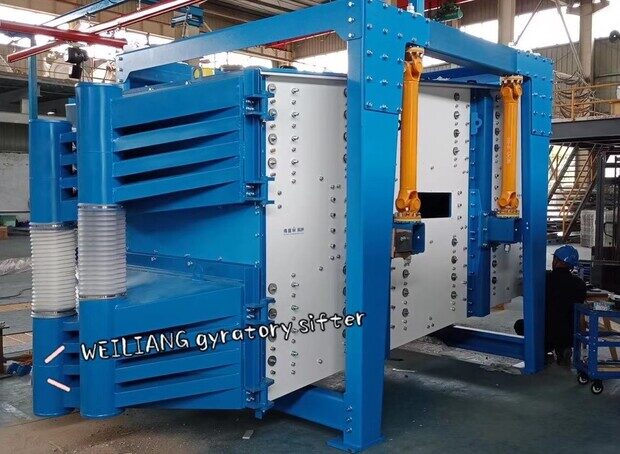
MANUFACTURING PROCESS OF SILICON POWDER
Turnkey projects, including the whole process of silicon powder production.
1) Feeding
2) Coarse crushing
3) Primary screening
4) Secondary crushing
5) Secondary screening
6) Storage
7) Conveying
8) Inspection
9) Dust removal
STRENGTHS OF WEILIANG
1. UPGRADED SIEVING EQUIPMENT
The new model has a 25% increase in single deck screening area compared to the old model and a 48% increase in overall screening area. 5 deck screens divide the material into six types, reducing the number of materials distributed on each deck and achieving a 98% screening rate and a 13% increase in relative screening efficiency.
2. UPDATED NEW LINE SYSTEM
The efficiency of the new line process system has been increased to 90%, a relative increase of 5% compared to the old line. The output of the new single line has increased to 13 t/h, compared to 3 t/h in the old line, a relative increase of 10 t/h.
3. ALL-ROUND SAFETY
Improve the overall level of equipment, reduce the failure rate, improve the equipment sealing of the whole system, and essentially eliminate the hidden danger of dust accumulation in the system.
The whole system is automatically controlled by DCS, with explosion-proof electrical, nitrogen protection, special anti-static equipment, lightning protection measures, and dustproof sealing measures for the bearings of rotating equipment.
A special iron removal device ensures that no foreign objects enter the crusher piping system. The conveying lining is made of wear-resistant resin polymer to ensure that the material does not come into contact with metal as far as possible. Explosion-proof ports are added at suitable locations, especially in the dust extraction system and in the silo.
Dust detectors are installed in the system to monitor the dust concentration in the process system in real time and to keep the dust concentration within 50% of the lower explosion limit. When the dust concentration exceeds the limit, the amount of nitrogen entering can be automatically adjusted to control the dust concentration.
4. EXTENSIVE EXPERIENCE
Weiliang has rich experience in the field of silicon powder screening, some of our cooperative customers such as Xin XX, Yuan XX, Zhong XX, Guo XX , Si XX etc.
We have helped customers solve various screening problems and establishing a solid reputation.
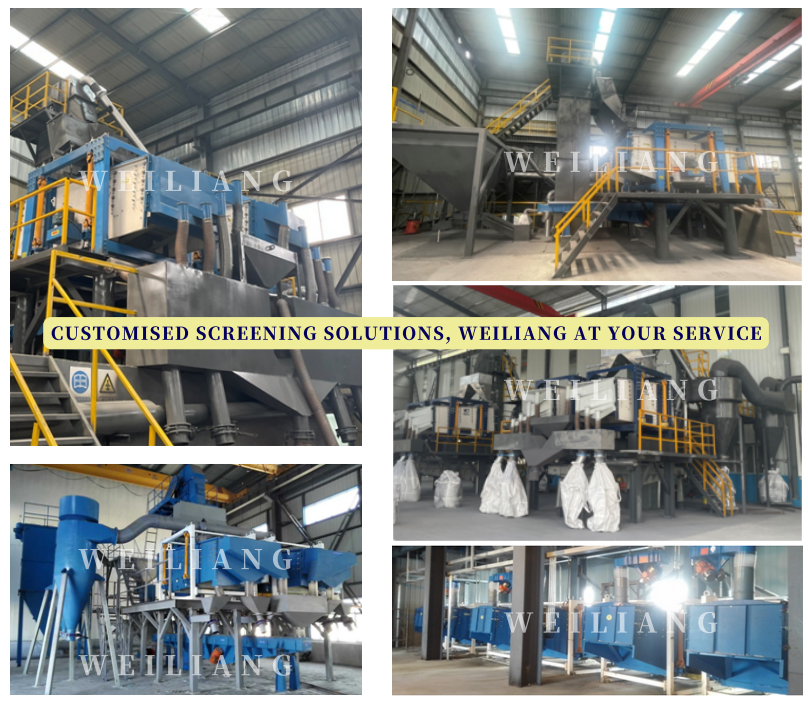
WEILIANG, First Manufacturer Owns the Fully-automatic Assembly Line for Gyratory Sifter.
Large capacity and high precision, WEILIANG gyratory screen plays a remarkable role in silicon powder screening.